The surface area in just one gram of activated carbon filters amazes me – it can cover 500 square meters! Picture two tennis courts side by side, and that’s what we’re talking about.
My experience shows these filters work incredibly well to purify both air and water because of their impressive adsorption power.
These filters excel at removing organic compounds, chlorine, and some heavy metals from water. They also do a great job eliminating VOCs and odors.
But they can’t handle everything. To name just one example, they won’t stop microbial contamination or filter out minerals like calcium and magnesium.
Let me walk you through how these filters clean contaminants, what they’re made of, and the best ways to keep them running smoothly.
This piece will give you everything you need to know about the technology. You’ll find it helpful whether you want to set up a water filtration system or just learn about how these filters work.

Fundamentals of Activated Carbon Structure
Activated carbon’s complex structure makes it an effective filtration medium. Its exceptional performance in capturing contaminants comes from its unique microporous architecture and surface chemistry.
Microporous Carbon Architecture
The structure of activated carbon has an array of slit-shaped pores that create a network of channels throughout the material [1].
These pores come in different sizes, from macropores to micropores. High-quality carbons have micropores that make up 70% to 90% of their total structure [2].
Steam or chemical treatment develops this complex pore network during activation.
Steam activation happens at temperatures between 800°C and 1000°C [3]. Chemical activation uses agents like phosphoric acid or zinc chloride at 500°C to 800°C [3].
Surface Area and Adsorption Sites
The most impressive feature of activated carbon is its massive surface area. A single pound of activated carbon gives you about 125 acres of surface area [4].
On top of that, a teaspoon of activated carbon has more surface area than a football field [4].
The activation process creates millions of microscopic pores that result in this extensive surface area [2].The carbon’s graphitic platelets are vital for capturing contaminants.
These platelets generate high adsorption potential energies when positioned close together [4].
The surface chemistry plays a big role in the filter’s performance, especially when you have oxygen-containing functional groups that boost moisture and contaminant capture [1].
Types of Carbon Materials Used
Three main source materials are used in activated carbon production:
- Coconut Shell Carbon
- Coal-Based Carbon
- Wood-Based Carbon
The choice of carbon material makes a big difference in filtration performance.
Manufacturers modify these base materials through various activation processes to create specialized products. Granular activated carbon (GAC) has loose granules that let water flow easily.
Carbon block contains fine granules held together with a bonding agent that takes up only 15% of the surface area [5].
As carbon grinding becomes finer, the available surface area grows and improves filtration efficiency [5].
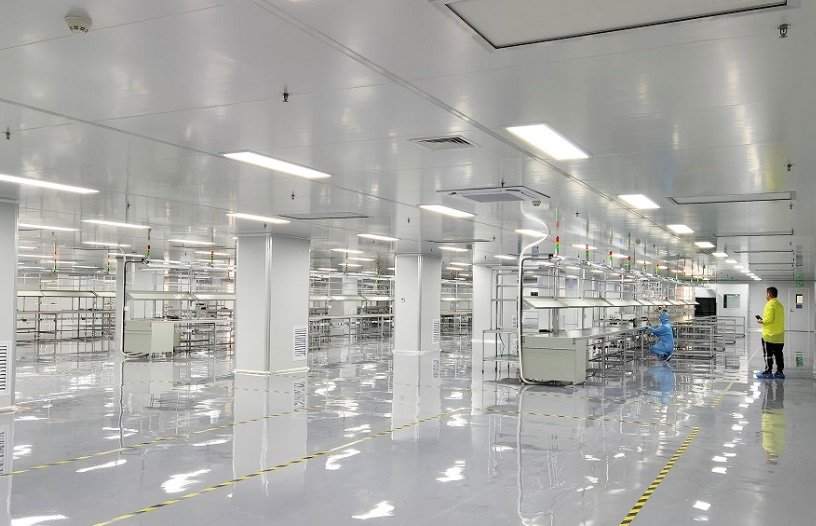
Chemical Process of Contaminant Capture
The difference between adsorption and absorption shows how activated carbon filters remove contaminants through a unique process.
Adsorption vs Absorption Mechanics
Activated carbon uses adsorption instead of absorption. A sponge absorbs by soaking up substances, but adsorption makes contaminants stick to the carbon’s outer surface [6].
The pollutants attach to the carbon’s exterior rather than going inside it [6].
This method helps activated carbon catch dissolved contaminants that affect water’s taste, smell, color and toxic content [7].
The carbon’s ability to catch contaminants depends on:
- The carbon’s physical features (surface area and pore layout)
- What the carbon is made from
- The contaminants’ chemical makeup and amount
- Water pH and temperature
- How long water stays in contact with the filter [8]
Molecular Binding Mechanisms
Two main processes make molecular binding work:
- Physical Adsorption (Physisorption)
Van der Waals forces power physical adsorption. These are the weakest forces between molecules [9]. They create close-range connections between the carbon surface and contaminant molecules. The carbon’s graphitic platelets turn neutral organic molecules into intra-molecular dipoles [7]. - Chemical Adsorption (Chemisorption)
Stronger chemical bonds form between the contaminant and carbon surface in this process [10]. The carbon can typically handle 10-20 pounds of contaminant per 100 pounds [11].
Molecular weight affects how well contaminants are captured. These systems work best with organic compounds weighing between 50 and 200 [11].
Molecules under 50 don’t stick well enough, while those over 200 bind too strongly and are hard to remove [11].
The filter stops working when the carbon reaches its full capacity [11]. At this point, thermal desorption or vacuum regeneration can restore the carbon’s ability to catch contaminants [11]. This cleanup happens on-site or off-site using high temperatures or low pressures [11].
Temperature and pH play a big role in how well adsorption works. Lower temperatures and pH levels usually mean better adsorption [8]. The carbon’s surface charge changes with pH and this affects how it catches different contaminants [8].
Breakthrough capacity tells us how much pollution the filter can handle before contaminated water starts coming through [11].
This is different from total saturation capacity, which shows the maximum amount of contaminants the carbon can hold [11]. The working capacity for each cycle is the space between breakthrough capacity and heel capacity – the leftover contaminants after cleaning [11].
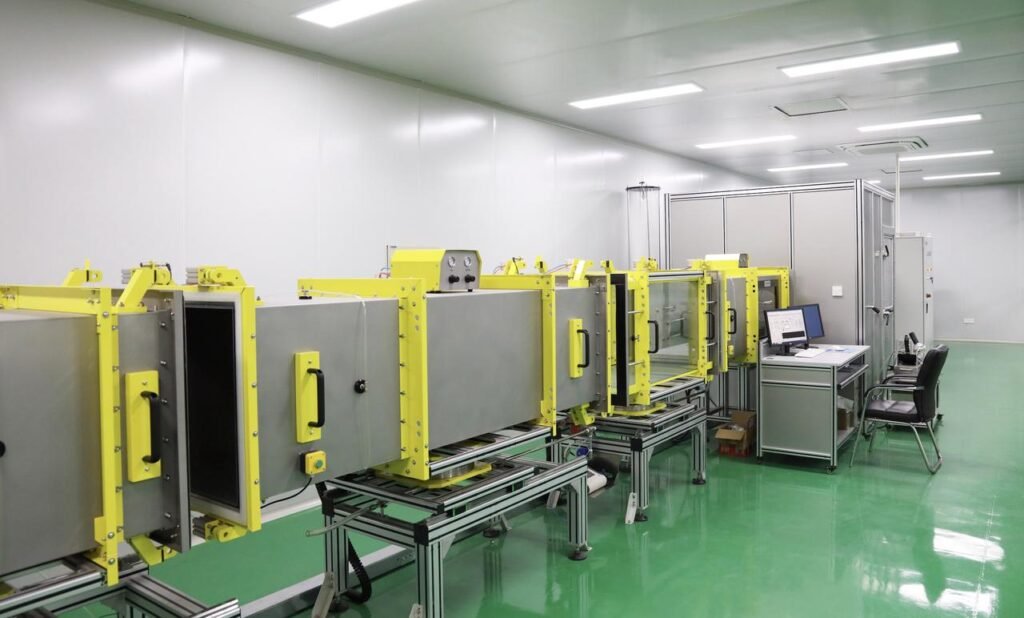
Activated Carbon Filter Components
Modern activated carbon filtration systems combine multiple components that remove contaminants effectively. These advanced systems use precise engineering to filter efficiently.
Filter Housing Design
The housing acts as the main containment structure. Manufacturers build it from 16-gage electro-galvanized steel [4].
They add corner gussets along the upstream side to make it more durable. Center stability bars strengthen housings wider than 24 inches [4].
The design has dual-sided access doors with positive tension locks. These create an airtight seal between the housing and door gaskets [4].
Industrial-grade housings fit both pre-filters and carbon trays. They feature 2-inch or 4-inch pleated pre-filters next to 3/4-inch refillable carbon compartments [4]. Permanent fastening processes make the housing structure stronger [4].
Carbon Bed Configuration
The carbon bed’s arrangement is vital to filtration success. Standard setups keep bed depths between 2 to 3 feet for simple applications.
These can extend to 6 feet for specialized treatments [12]. The bed design leaves 50% freeboard space to make backwashing operations easier [12].
Carbon beds use a strategic layering approach:
- Top layer: Smaller sized particles
- Middle section: Medium-sized granules
- Bottom layer: Largest particles [7]
This layered setup captures contaminants while maintaining proper flow distribution. The bed typically runs at velocities between 0.05-0.5 meters per second. These speeds ensure heat dissipates properly and prevent preferential flow patterns [13].
Flow Control Systems
The flow control mechanism combines several key components:
- Blowers for air movement
- Electrical control systems
- Air ducting networks
- Temperature alarm systems
- Pressure gages
- Regeneration valves [1]
The system runs within specific parameters. Air velocities range from 50 to 75 feet per minute (0.25 to 0.38 m/s) [1]. Contact time, also known as empty bed residence time (EBRT), usually lasts between 2.5 to 4.0 seconds to remove contaminants effectively [1].
Manometers and H2S detectors help monitor performance [1]. The flow setup often uses a lead-and-lag bed arrangement.
This maximizes treated water volume per pound of activated carbon [7]. The sequential series setup removes contaminants thoroughly while using carbon efficiently.
The design keeps relative humidity levels below 70% at the carbon bed contact point. This helps remove organic compounds effectively [13].
Air treatment applications need dust concentration below 1mg/Nm³ when using extruded or granular activated carbon [13].
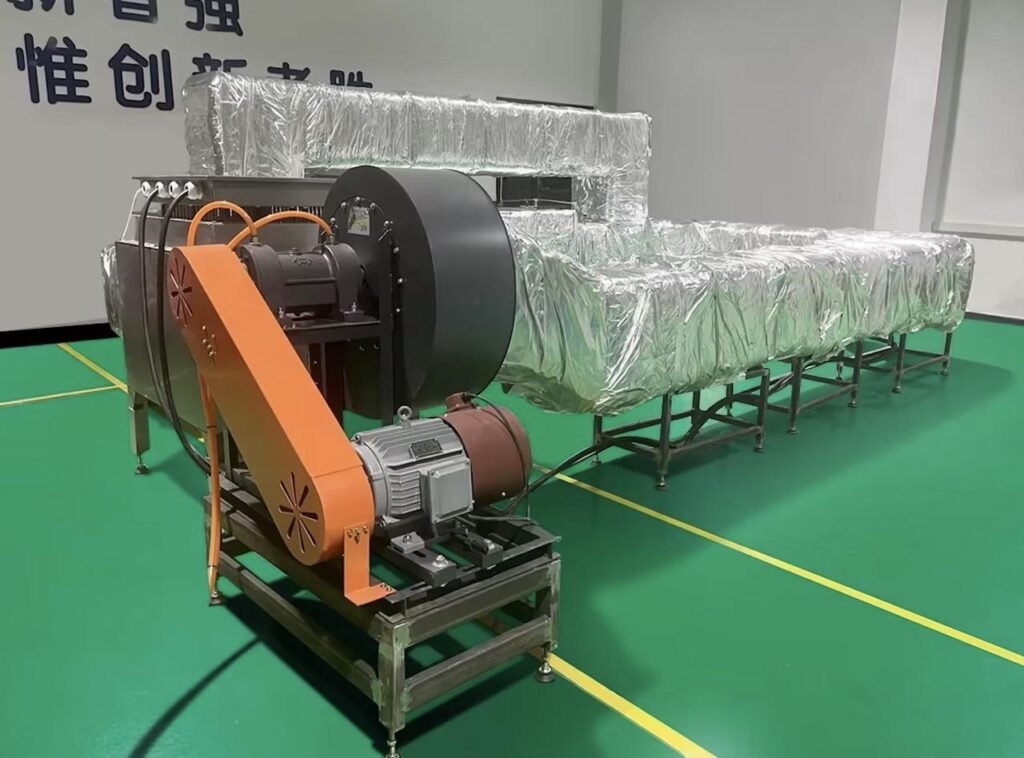
Performance Metrics and Testing
Scientists need rigorous testing protocols and precise performance metrics to measure how well activated carbon filters work. Laboratory analysis and field testing help determine filtration success rates through specific parameters.
Removal Efficiency Rates
Activated carbon filters show different removal efficiencies based on several factors. Research suggests removal rates from 67% to 100% for various contaminants [14]. All the same, these rates change based on:
- Filter age and regeneration status
- Contaminant molecular structure
- Water temperature and pH levels
- Flow rate variations
Removal efficiency reaches 69% for KMnO4, 53% for TOC, and 77% for UV254 with organic compounds [15]. High molecular weight compounds show almost complete removal. Low molecular weight substances are harder to filter [15].
The iodine test and phenol test are key indicators of adsorption capacity. The iodine number, measured in milligrams per gram of carbon, associates with the filter’s adsorption potential.
Higher numbers show greater adsorption capability [5]. The phenol number has an inverse relationship to organic removal capacity. Lower values mean better performance [5].
Contact Time Requirements
Empty Bed Contact Time (EBCT) plays a key role in filtration effectiveness. Scientists calculate EBCT by dividing empty bed volume by design flow rate [14]. Research shows that reducing flow rates by 10 L/s (from 39 to 29 L/s) boosts total removal efficiency by:
- 14% in older filters
- 6.5% in newer filters [2]
Temperature affects contact time because:
- Higher temperatures decrease solution viscosity
- Increased temperatures can speed up diffusion rates
- Lower temperatures often lead to better adsorption [12]
Breakthrough Point Detection
Breakthrough detection is crucial for filter monitoring. The breakthrough point happens when contaminants saturate all adsorption sites [16]. Modern detection methods include:
- Continuous effluent monitoring
- Regular water quality testing
- Pressure differential measurements
- Breakthrough curve analysis
Different compounds show varying operation half-times. PFCAs display distinct patterns:
- PFHxA reaches 50% removal at 20,300 bed volumes
- PFOA stays effective until 68,300 bed volumes [2]
PFSAs last even longer:
- PFBS: 22,300 bed volumes
- PFHxS: 91,600 bed volumes
- PFOS: 284,000 bed volumes [2]
Filter performance needs testing every three to six months [17]. Breakthrough curves help predict when filters need replacement. CFD modeling helps estimate concentration changes throughout the filter and optimizes processes [18].
Breakthrough capacity is not the same as total saturation capacity. The gap between breakthrough and heel capacity defines each cycle’s working capacity [12].
Filter replacement should happen before target substances exceed the Maximum Contaminant Level (MCL) [14]. Teams usually start the changeout when effluent concentration hits half the MCL value [14].

System Maintenance Requirements
Your activated carbon filtration system needs proper maintenance to work at its best. Good upkeep will help your filters last longer and remove contaminants better.
Filter Replacement Intervals
Several factors determine how long activated carbon filters last. Standard filters should be replaced every 3-6 months according to manufacturer guidelines [19]. Large industrial systems with backwashing capabilities can last anywhere from 1-10 years [20].
These factors affect how often you need replacements:
- Water Quality Parameters
- Filters need more frequent changes with dirtier water
- Pre-filtered water makes carbon filters last longer [3]
- Water temperature changes how well filters absorb contaminants
- Usage Volume
- Heavy use wears filters out faster
- Industrial systems need custom replacement schedules [21]
- Changes in flow rate affect filter life
Granular activated carbon (GAC) systems usually need new filters every 6-12 months [20]. Sintered activated carbon filters also work well for 6-12 months. They’re best at removing heterochromia, odor, and leftover chlorine [20].
Performance Monitoring Methods
You need several approaches to check if your filters work right. Here are the main things to watch:
- VOC levels at the adsorber outlet
- When to run regeneration cycles
- How active the carbon bed is
- The bed’s temperature
- Incoming gas temperature
- Gas flow rate
- Pressure differences [11]
Modern monitoring uses spectral induced polarization (SIP) to get up-to-the-minute data analysis. This method checks filter performance by injecting alternating current at 0.01−103 Hz frequencies [6].
Here’s what you need to do for the best maintenance:
- Regular Assessment
- Watch for water quality changes
- Look at pressure differences
- Check flow rates often
- Look for visible debris [3]
- Preventive Measures
- Clean pre-filters often
- Keep water quality steady
- Maintain correct flow rates
- Keep records of performance [3]
Steam or chemicals help keep carbon beds clean [21]. The mechanical parts need replacement along with media changes. A good preventive maintenance plan helps avoid unexpected breakdowns and meets regulations [21].
The activated carbon tester (AC tester) is a great way to check filter performance. This simple method needs minimal equipment but tells you a lot about your filter’s condition [10]. Expert advice suggests using these tests with official AWWA and ASTM methods to get a detailed assessment [10].
Breakthrough detection helps you spot problems quickly. Filters that are full show slower flow rates, water discoloration, or crumbly bits [22]. Quick action when you see these signs prevents damage and keeps your filters working well.

Conclusion
Activated carbon filtration is a remarkable technology that combines intricate structural design with powerful contaminant removal capabilities.
My research shows these filters work best at removing organic compounds, chlorine, and certain heavy metals. The system’s maintenance requirements remain straightforward.
These filters’ success depends on several elements working together:
- Microporous structure that provides massive surface area to capture contaminants
- Specific adsorption mechanisms that target different molecular sizes
- Carefully engineered housing and flow control systems
- Regular monitoring and maintenance protocols
Users can maximize their filter’s performance and longevity by understanding these elements.
My tests reveal that proper maintenance, timely replacements and consistent monitoring extend the filter’s life substantially. The system maintains optimal contaminant removal rates with proper care.
The technology keeps advancing, though it has its limits. Activated carbon removes many contaminants well but doesn’t deal very well with all water quality issues alone.
Users should think over their specific filtration needs. Sometimes combining technologies becomes essential to create detailed water treatment solutions.
This detailed look at activated carbon filtration shows why it remains the life-blood of modern water and air purification.
These systems prove valuable in residential and industrial applications because they combine proven effectiveness with simple maintenance and reliable performance.

FAQs
Q1. How does activated carbon remove contaminants from water?
Activated carbon removes contaminants through adsorption. As water passes through the filter, chemicals and organic matter are trapped on the carbon’s vast surface area, which is created by millions of microscopic pores. This process effectively removes many dissolved substances, improving water quality.
Q2. What types of contaminants can activated carbon filters remove?
Activated carbon filters are highly effective at removing organic compounds, chlorine, and certain heavy metals. They can eliminate up to 99 percent of total suspended solids, volatile organic compounds, sediment, and other contaminants that affect taste, odor, and color of water.
Q3. How often should activated carbon filters be replaced?
The replacement frequency for activated carbon filters varies depending on usage and water quality. Generally, standard filters should be replaced every 3-6 months. However, larger industrial systems may last between 1-10 years. Regular monitoring of water quality and filter performance is crucial to determine the optimal replacement time.
Q4. Can activated carbon filters remove all types of contaminants?
While activated carbon filters are highly effective for many contaminants, they cannot remove all types. They are not effective against microbial contamination or minerals like calcium and magnesium. For comprehensive water treatment, it may be necessary to combine activated carbon with other filtration technologies.
Q5. How can I tell if my activated carbon filter needs replacement?
Signs that your activated carbon filter may need replacement include reduced water flow, discolored water, or the presence of crumbly residues. Additionally, if you notice changes in water taste or odor, it could indicate that the filter has reached its saturation point and needs to be replaced.
References
[1] – https://pdhacademy.com/wp-content/uploads/2023/09/437-Activated-Carbon-Odor-Control-Systems.pdf
[2] – https://www.sciencedirect.com/science/article/pii/S0043135420304504
[3] – https://www.dubaopump.com/info-detail/maintenance-and-replacement-cycle-of-activated-carbon-filter
[4] – https://www.filtrationgroupiaq.com/wp-content/uploads/2020/08/FG-IAQ-_-Carbon-Sorb-Housing-1.pdf
[5] – https://ag.umass.edu/cafe/fact-sheets/activated-carbon-treatment-for-drinking-water-supplies
[6] – https://www.sciencedirect.com/science/article/abs/pii/S0043135422000665
[7] – https://www.watertechonline.com/wastewater/article/15549902/the-basics-of-activated-carbon-adsorption
[8] – https://www.waterprofessionals.com/learning-center/activated-carbon-filters/
[9] – https://rajahfiltertechnics.com/uncategorized/the-science-behind-activated-carbon-how-it-works-and-why-its-effective/
[10] – https://wcponline.com/2009/10/19/monitoring-activated-carbon-drinking-water-filters/
[11] – https://www.epa.gov/air-emissions-monitoring-knowledge-base/monitoring-control-technique-activated-carbon-adsorber
[12] – https://www.watertreatmentguide.com/activated_carbon_filtration.htm
[13] – https://services.jacobi.net/design-selection-of-air-gas-treatment-with-industrial-filters/
[14] – https://www.health.ny.gov/environmental/water/drinking/docs/interim_recommendations_for_granular_activated_carbon_installations_v_1.pdf
[15] – https://www.sciencedirect.com/science/article/abs/pii/S0160412005001273
[16] – https://extensionpubs.unl.edu/publication/g1489/na/html/view
[17] – https://wcponline.com/2014/06/17/evaluation-activated-carbon-performance/
[18] – https://www.sciencedirect.com/science/article/abs/pii/S0263876224003137
[19] – https://pristinewatersofteners.com/activated-carbon-water-filters-lifespan-and-when-to-replace-them/
[20] – https://www.quora.com/How-often-does-activated-carbon-need-to-be-replaced
[21] – https://complete-water.com/blog/when-should-i-service-my-carbon-filter
[22] – https://abhirowater.com/when-to-change-your-activated-carbon-filter/